Introduction: D-LBFG Discus Launch Balsa Free Flight Glider
This Discus Launch balsa free flight glider build is for the aspiring aero modeller that is no longer satisfied by flying his foam chuck gliders but is not quite yet feeling confident enough to Build a complex wooden model aircraft kit. However this build might also interest the experienced RC model aviator who has crashed all his planes for the season but desperately needs to fly and is left only with a few Balsa boards and salvaged electronics. In this build we will discover the wonderful material balsa wood and go over the basic building techniques, tips and tricks in aero modelling.
Step 1: Bill of Materials
- Glider parts plan printed on 120 g/m^2 printer paper
- 2x 3 mm Standard Balsa wood board 100x1000 mm
- 2 mm Standard Balsa wood board 100x550 mm (optional use of 2 mm birch aircraft plywood)
- 1 mm Standard Balsa wood board 100x300 mm (optional use of 1 mm birch aircraft plywood)
- 5 mm diameter dowel (wood or other) (Optional use of two 5x4 mm cylindrical magnets and metal washers)
- Universal Adhesive Fe Tire Balance Weights 5g (optional use of lead shot)
- Optional: Leftover fiberglass scraps
Step 2: Tools and Consumables
- Cutter and/or scalpel
- Pins or needles
- Painter’s tape - Ruler or straight edge
- Sanding blocks covered with 60, 120 and 250 grit sandpaper
- Balsa wood glue (UHU Hart or other)
- Wax baking paper
Optional:
- 400 grit sandpaper
- CA-Glue
- Reversible spray mount
- Coping saw
Step 3: Parts Plan
Print out the parts plan on 120 g/m^2 printer paper. If you are like me and don’t possess a plotter, I have also provided a parts plan tiled on A4 paper in the files section of this build. Just make sure to print the plans in 100% scale in your printer dialog.
To assemble the plan, cut along the red dashed line using a Ruler and scalpel, then tape together the individual sections using the Painter’s tape on the back side of the plans.
Next, cut out the individual part plans for the different Balsa wood boards.
It is important to note here that patience and precision go hand in hand and will take you a long way. However, this can also be said for the rest of the build and aero modelling in general. So take your time and focus.
Step 4: Fix Plans and Cutting Parts
Glue the individual part plans onto their corresponding balsa wood boards. I used reversible spray mount for this as it provides enough tack for cutting out the pieces without leaving residue or taring the balsa wood when peeled off. However, you could also use a glue stick or cut out the parts and trace them onto the balsa wood.
Then, cut out the balsa glider parts on a cutting mat or work surface using a sharp cutter blade and/or scalpel for added precision. Here you will see how soft and lovely the material is to work with. The more complex radiuses and corners can also be carved. Just make sure to be careful when cutting perpendicular to the wood grain as to not chip it. In this, the sharpness of your blade is paramount.
Make sure to only peel of the paper templates when the parts are needed, to not lose track of the part numbers.
One thing to note is to refrain from rearranging the parts as they are nested as is to account for the grain direction of standard balsa wood boards. This is important for the stiffness of the corresponding glider parts in their load direction.
Here you might also want to decide if it is worth the extra cost and effort (sawing out with a coping saw) for you to use the optional birch aircraft plywood boards, as this will greatly improve the stiffness and durability of the glider.
Step 5: Pre-assembly Fuselage
Pre arrange parts 1-7 in their corresponding order. Then separately glue together the right side cockpit parts 1 & 2, the fuselage parts 3-5 and the left side cockpit parts 6 & 7. Do this by coating each side to be glued with an even film of UHU Hart glue. In this make sure that in each pre-assembly the thiner wooden parts face outwards corresponding to their final assembly position. This can be seen in the full-scale drawing of the glider.
Then, weight them down on a flat building surface whilst the glue is curing. This is to ensure that all parts are glued up straight without a twist or bend in them and to squeeze out any excess Glue. Make sure that the parts don’t slip whilst the glue is curing. Generally, you can use the Wax baking paper for the glueing steps, if you are worried about glue residue on your work surface.
Here I would like to add a few words about different glues. In aero modelling great care has to be taken to use the right glue as well as amount for each application. For gluing balsa wood I would strongly recommend the use of a special glue like UHU Hart wich is specifically tapered to this material and application.
You can also use CA-Glue to speed up the build. However, with this it is easy to make mistakes when positioning the parts and or gluing them up with a twist or bend, as you don’t have the time to correct anything. Also CA-Glue is quite hard compared with the soft Balsa wood, meaning that there is a potential for stress fractures between the two materials. Using standard wood glue is not recommended. Firstly, due to the material property (hardness and weight) but also, mainly because of the moisture content wich easily warps the Balsa in the process.
Step 6: Fuselage Assembly
Glue the right side cockpit pre-assembly (parts 1 & 2) to the fuselage pre-assembly (parts 3-5). Then weight them down on a flat building surface whilst the glue is curing.
Step 7: Left Cockpit Latch Mount
Glue 5 mm long cut-offs of the dowel into the fuselage assembly. These will hold the left cockpit latch with a friction fit, so you can later access the ballast chamber in the fuselage.
Optionally you could use 5x4 mm cylindrical magnets and thin metal washers with a 5 mm diameter for this to provide a more secure and wear resistant mount.
Step 8: Wing Assembly
Glue together parts 8 & 9 as well as 10 & 11 to form the gauge blocks for the wing assembly.
Use the gauge blocks to prop up each wing (parts 12 & 13) to sand an angle where the wings will be joined to ensure they are glued up flush.
Glue up the wings with UHU Hart using the gauge blocks. To ensure a flush and straight glue up, first join the wings on the under side with a piece of Painter’s tape.
Step 9: Dry Fit
Dry fit the fuselage with the wings, rudder (part 14) and elevator (part 15) and mark with a pencil where the flying surfaces will join to the fuselage.
Step 10: Everyones Favourite Step… SANDING
In all earnest sanding is probably the most annoying, seemingly useless, step in every build. However, taking time and care here will really pay of at the end when you are holding a glider with nice smoothly sanded finish in your hands.
On this glider, we will round almost every corner. Here is a very simple method to create nice, evenly rounded corners.
First, sand a 45 degree chamfer half way through the thickness of your material (or radius) as illustrated. Then, chamfer each of the 2 new edges splitting the angle. Finally, round of the chamfers completely with smooth strokes along the radius.
Don’t be afraid to use very coarse grit sandpaper for the first two sanding operations, especially, with the soft balsa wood. In my experience, this yields and more accurate shape than finer sandpaper, which usually promotes using uneven sanding pressure and more uncoordinated sanding strokes.
Step 11: More SANDING ;-P
Round of all corners on the parts using the described method except for the previously marked out areas where the fuselage joins to the flying surfaces.
Additionally, flatten the underside of the wings where they will be glued to the fuselage being careful not to break them apart.
After shaping all edges work your way through the different sand paper grits to smooth the parts. Finish with a 400 grit sandpaper by also soothing the flat surfaces for a nice finish. This will not really impact the aerodynamics or anything else but boy will it yield a satisfying finish.
Now we are ready for the final assembly!
Step 12: Final Assembly
Glue up the fuselage with the rudder (part 14), elevator (part 15), wings and wingtips (parts 16 & 17) using generous amounts of UHU Hart use pins or needles to hold the pieces in place while the glue is curing. Take care to make sure that the elevator and rudder are perpendicular to each other and line up with the wings as shown. Wipe off any excess glue seeping out.
Generally speaking there can never be enough pins or clamps when gluing something up, however, be careful not to turn your model into Swiss cheese.
Step 13: Preparing Reinforcements
Cut out and fold the paper reinforcements (parts 18-24). Alternatively, you could use them as templates to cut these parts out of fibre reinforcements such as fibreglass, if you have some lying around, as this will definitely be stronger.
Step 14: Applying Reinforcements
Apply the reinforcements using CA-Glue to the upper and lower sides of the wings and fuselage as well as the wing tips.
If wanted you could now give your glider a final sanding…
Step 15: Decorations
The plans provide paper templates for a canopy (parts 25-27) which can be glued to the fuselage. Alternatively, you can use them like me to trace the canopy onto the fuselage with a permanent marker and the shading it.
However, this step is really up to your preferences.
Step 16: Center of Gravity
The center of gravity or CG of a glider or an aircraft marks a theoretical point where the aircraft should be balanced for the optimal flight characteristics. The exact CG will vary for each glider built, however, as a starting reference the CG of this glider should roughly be 30 mm from the trailing edge of the wing.
As a tip, to mark this spot for easy reference out in the field, I usually use two cut off pinheads stuck under the wings, to balance the glider on my finger tips. These can be glued into place when the exact CG location has been found.
Step 17: Add Trimming Ballast
To balance your glider on the provisional CG, add a universal adhesive tire balance weights to the ballast chamber in the nose of the glider. I used two stacks of two 5 g weights in the shown location. However, this will vary according to the density of your balsa and the amount of glue you used. So just add, subtract and slide the weights around until an equilibrium has been reached where the nose of the aircraft is pitched sightly downwards.
Alternatively you could also use lead shot glued into the ballast chamber. However, universal adhesive tire balance weights are dirt cheap and ideal for this application. Often times mechanics will even readily give you used ones for free if you ask them nicely.
Step 18: Finished Glider
With this your discus launch balsa free flight glider is complete and ready for its first flight. Take a moment to admire your work.
Don’t miss out on this step!
Step 19: First Flight and Trimming
For your first flights chuck the glider gently straight into the wind. Refrain from throwing it up high or down low with force as neither will result in a flight path that will show you the flight characteristics you are looking for.
If the CG of the glider is in the right place your glider should fly in a straight line gently towards the ground.
If the flightpath of your glider follows an upward curve leading to sudden pitch down manoeuvres, your CG is too far back. Counteract this by adding trimming ballast or sliding it forwards.
If the flightpath of your glider follows a downward curve, your CG is too far in front. Counteract this by subtracting trimming ballast or sliding it backwards.
If you are flying in very windy conditions, you might consider adding ballast directly under your CG to increase the wing loading on your glider resulting in a faster, more stable flight.
In this Please chose your airfield wisely (open, flat and empty spaces). Take care of your surroundings. Check regulations concerning model aviation in your country and your intended flying area. You are liable for what your glider does.
Step 20: Discus Launch
If you’ve been wondering all along what the heck is a discus launch is well, here’s your answer and a video explanation of how it works by someone who is much better at it than me.
Step 21: Picking Up the Pieces
Inevitably, sooner or later (mostly sooner) something will give and you will crash your glider. Remember step 16...
Please don’t be disheartened by this. It happens to the best of us, is part of model aviation and only very rarely is it not fixable. By the time my first balsa glider flew properly it was made of more glue than wood. Reparations are part of the process.
Step 22: RC Conversion
To the experienced RC model aviator who has crashed all his planes for the season but desperately needs to fly. Im sure you will be able to follow this build with ease and make the necessary adjustments for an RC conversion along the way according to the RC conversion plans and drawings.
One thing to note is to make sure to add the rudder bevel according to your throwing arm.
The use of birch aircraft plywood is definitely necessary.
The rudder and elevator are meant to be linked up with a simple DLG pull spring system and the ailerons can simply be connected with some bent spring steel.
Step 23: Files
Here are the part plans and glider drawings as PDF vector files.
P.S. For those of you in possession of, or with access to a laser cutter you can probably extract the paths and save yourself the cuttings.
Step 24: Files RC Conversion
Here are the part plans and glider drawings for the RC Conversion as PDF vector files.
P.S. For those of you in possession of, or with access to a laser cutter you can probably extract the paths and save yourself the cuttings.
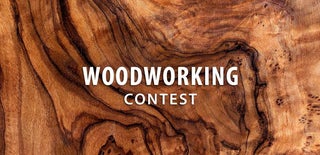
Runner Up in the
Woodworking Contest